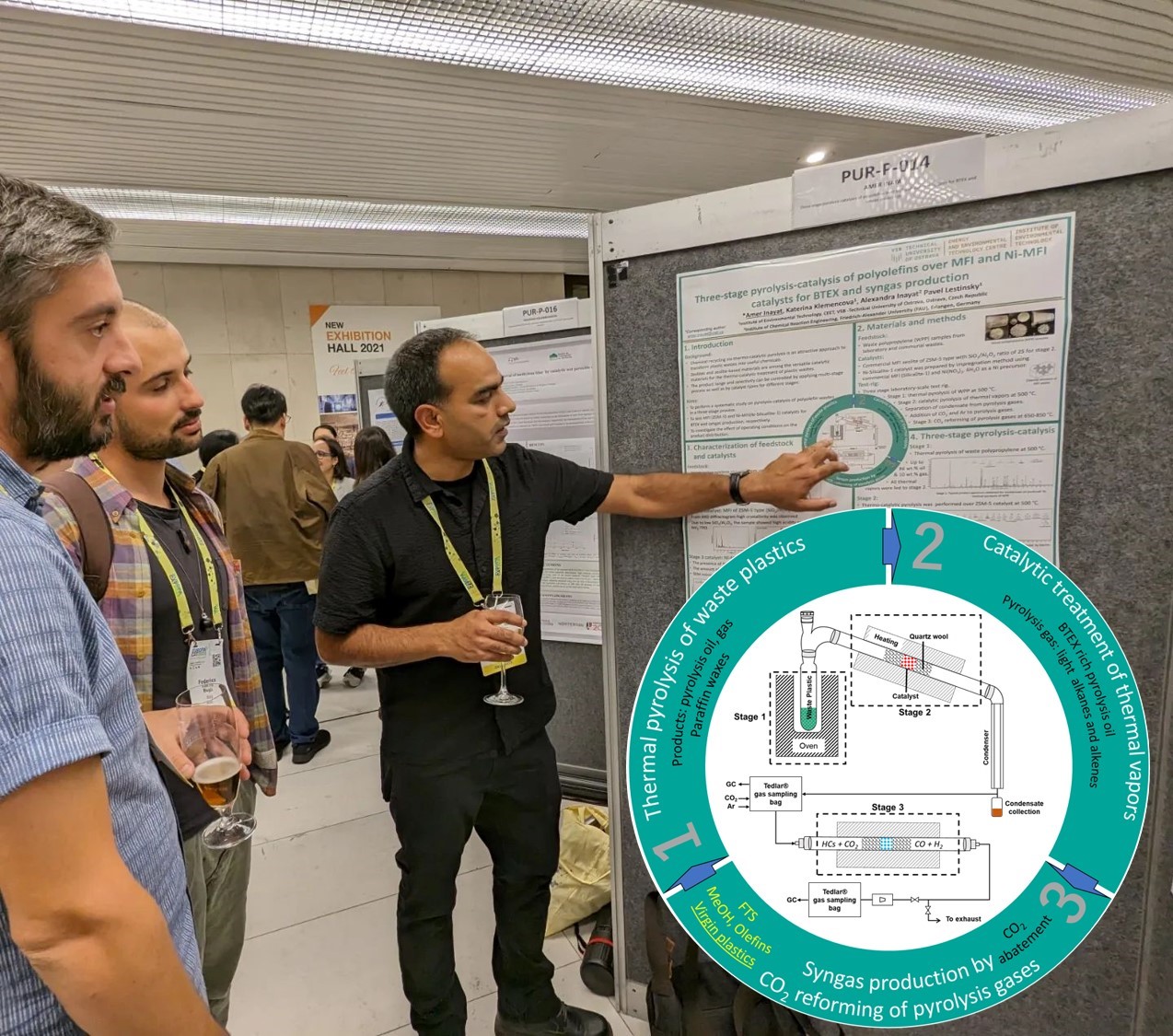
A cutting-edge method utilises waste plastics and carbon dioxide to generate hydrogen and other valuable materials
A new three-step process, designed and tested by researchers from the Institute of Environmental Technology (IET) of VSB-TUO in collaboration with colleagues from Friedrich-Alexander University Erlangen-Nürnberg (FAU), Germany, utilises waste plastics and carbon dioxide to produce hydrogen and other useful chemicals for applications in the chemical or petrochemical industries. The researchers believe the method could help decrease reliance on fossil resources and reduce waste. The study published in the prestigious journal Fuel offers valuable insights for advancing chemical recycling processes and carbon dioxide utilisation.
The idea for the three-stage process, consisting of pyrolysis, catalytic refinement of pyrolysis vapours, and subsequent dry reforming of the pyrolysis gas, was conceived by one of the paper’s authors about a year ago when presented as a “proof of concept” at the EuropaCat 2023 international catalytic conference in Prague. In the following months, he and his colleagues in the laboratory optimized the experimental setup, process conditions, and catalysts. Polypropylene, a common packaging material used in the food industry, was utilised for the experiments. However, the researchers also plan to test other types of plastics in the future.
“We have created a three-stage system where in the first stage, thermochemical decomposition of waste plastics occurs, resulting in the formation of organic vapors and gases with low hydrogen content. These then pass through the first catalyst, where catalytic cracking and hydrocarbon aromatization occur. In order to obtain a larger amount of hydrogen, we decided to transform the obtained gas and carry out a dry reforming reaction in the third stage. The gaseous products were separated after the second stage, mixed with carbon dioxide, and passed through the second catalyst to obtain synthesis gas. This upgraded the pyrolysis gas while simultaneously disposing of carbon dioxide,” described the procedure one of the members of the authoring team, Pavel Lestinsky from IET, part of the Centre for Energy and Environmental Technologies at VSB-TUO.
He believes that the key to success is the integration of three processes that have been studied in the Industrial Chemistry laboratory at IET for more than five years. These processes ensure that the reaction runs smoothly without the deactivation of catalysts, unlike in other methods. At the end of the three-stage process, researchers obtain pure synthesis gas that contains only hydrogen and carbon monoxide which can be further utilised in the chemical industry. “We have inserted a step into commonly used methods where we first produce aromatic hydrocarbons which we separate. We then lead the clean pyrolysis gas without liquid substances, which would cause catalyst coking, to the reforming step. As a result, the reaction proceeds smoothly and we avoid problems with catalyst deactivation and reduced conversion,” Lestinsky added. According to him, the results were also achieved thanks to the use of the large research infrastructure ENREGAT and support from the REFRESH project.
The article built on the previous works by IET that focused on the chemical recycling of waste plastics or catalytic transformation of pyrolysis gases. The long-term goal of local researchers is to use plastic waste to obtain chemical substances that will be used to produce other types of plastics or as raw materials for the chemical industry. Researchers are actively seeking new possibilities and approaches due to the growing stringency of environmental regulations on carbon dioxide emissions, posing a major challenge.
https://www.sciencedirect.com/science/article/pii/S0016236124011232